'Scale Up' Rules
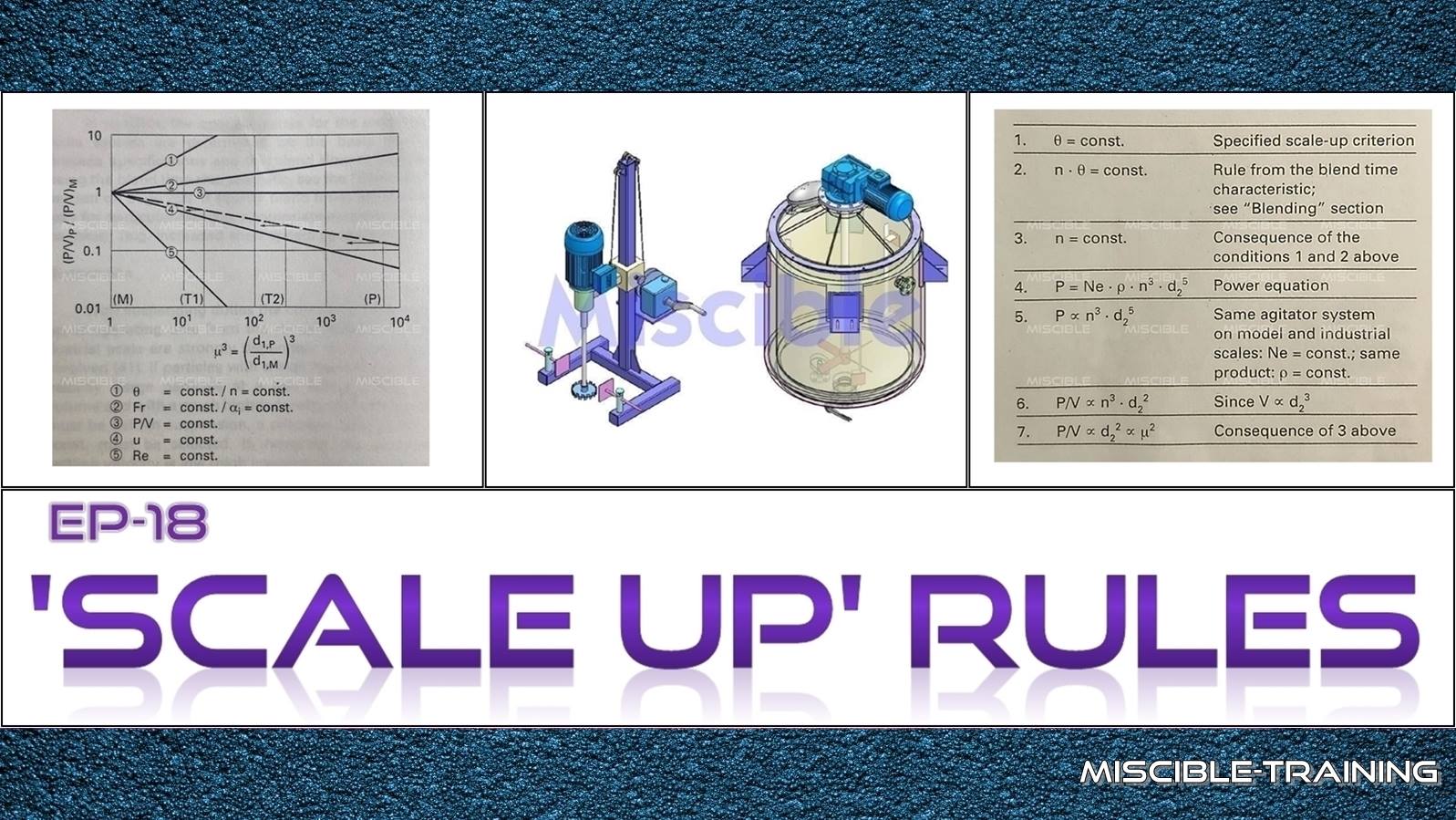
EP-18 : 'Scale Up' Rules
[HEAT TRANSFER]
It is normal practice only to check out the heat transfer coefficient of the agitator system under consideration at its full-scale dimensions., If the value of "film heat transfer coefficient" that is determined is insufficiently high, this can be improved by increasing the agitator power or by providing additional heat transfer surfaces. For duties that require the vessel contents to be cooled an optimization problem arises, since although increasing the power per unit volume increases the film coefficient "film heat transfer coefficient" , this also means that the increased energy input from the agitator requires additional heat to be removed. Values of "film heat transfer coefficient" can be calculated using the heat transfer characteristic as described in the “Heat transfer”.
During scale-up it must be taken into account that the vessel volume increases proportionately to the cube of the scale-up factor while the vessel surface area available for heat transfer increases in proportion to its square. If the scale-up is performed with a criterion “less” than "film heat transfer coefficient" = const. due to process constraints (P/V "film heat transfer coefficient" ? <0.5), the heat transfer capability is diminished not only due to the higher heat flux per unit area but also by the lower values of "film heat transfer coefficient"
[BLENDING]
From the Penney diagram it can be seen that for blend time = const, it is necessary to increase th power in put per unit volume by u^2, The effective power input therefore for a scale up of 'u' =10 is icreased by factor of 10^5, Following this rule to the letter would result in agtator systems with astronomic prices and alarming operating cost. In practice, However, it is nearly always unnecessary to apply this criterion, if the considerably loger batch times on an industrial scale are compared with the blend time necessitated by the process itself.
for Example :
an increase in blend time on industrial scale by a factor 5 times that on a model scale can be tolerated, the required power input is only 1/125 of that witch would have been necessary had the 'Blend Time = Cost", Rule been rigorously applied.
[SUSPENSION]
With suspending duties the criteria for the scale up of operating data from the model scale to an industrial scale are strongly dependent on the product involved. If particles with a high hindered settling velocity (large particles at a low concentration by volume and with a much higher density than the liquid) must be held in suspension, a criterion close to P/V= const. must be selected. If, however, the hindered settling velocity is low (high concentration by volume, small particle diameter, differential density low), a criterion approximating to u = const. can be considered as reasonable. Depending on the duty concerned, therefore, a broad spectrum of criterion from u = const. to P/V = const. may be relevant. There are therefore large differences in the power inputs required on an industrial scale.
To date there is no reliable knowledge of the relationship available on this subject, and therefore no “design equations” based on the operating data and physical properties. It is only the accurate knowledge of the efficacy of the various agitator systems and rheology of the individual media, based on results from model, pilot-scale and industrial-scale systems that makes it possible to select the optimum scale-up rules to be applied. If relevant operational experience is not available, an extensive series of tests in vessels of differing sizes must be carried out for the duty concerned.
[DISPERSING]
With this process the main objective is to produce the same interfacial areas per unit volume on both scales, in order to achieve the same mass transfer. The analysis based on turbulence theory has been confirmed by the knowledge gained in the form of the scale-up criterion P/V = const. This applies to dispersing processes in liquid/liquid and gas/liquid systems. Because of the numerous factors that influence the process (e.g. coalescence properties, physical properties of mixtures, anomalous flow characteristics, static pressure, etc.) substantial deviations from the theoretical results occur on scale-up! It is therefore extremely rare that a reliable prediction of the mass transfer coefficients achievable on an industrial scale can be made.
Cr. สถาพร เลี้ยงศิริกูล
Tel : 091.7400.555
Line : sataporn.miscible
Miscible Technology Co.,Ltd.